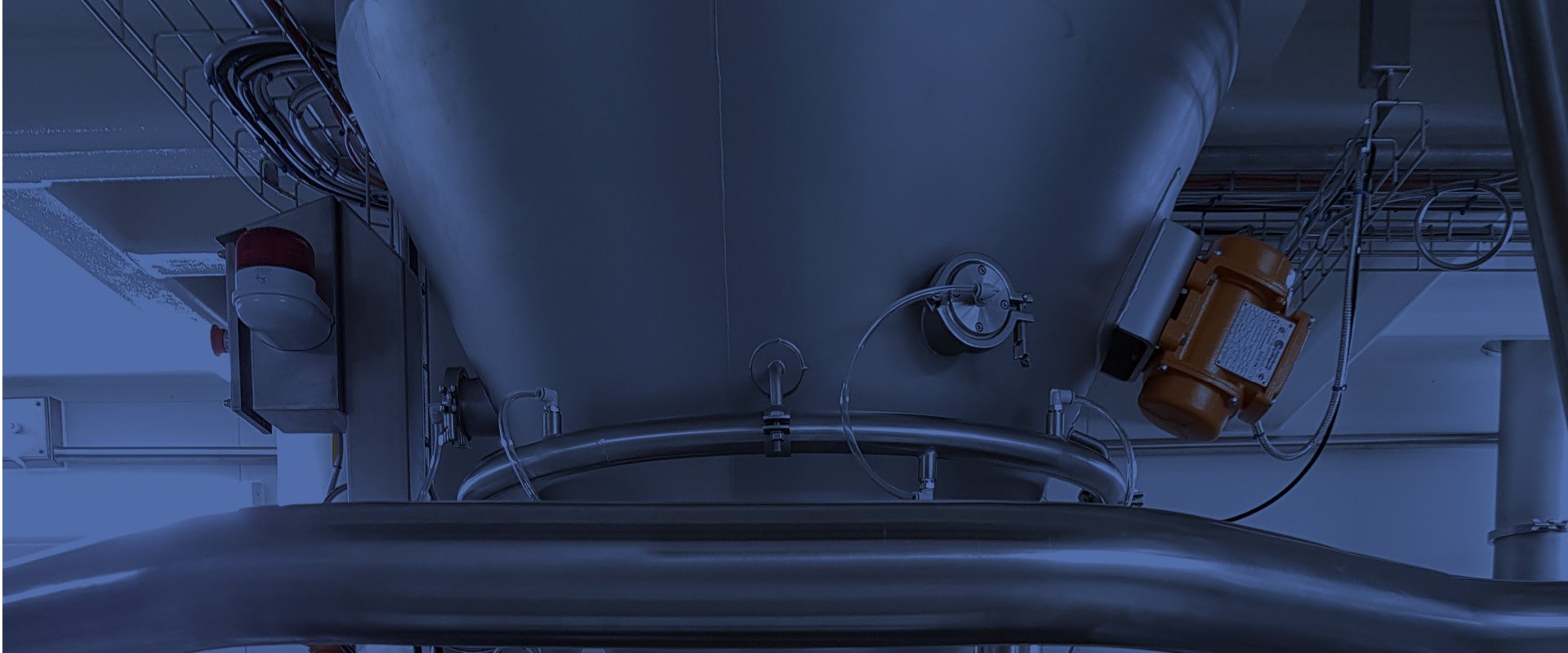
We are continuously challenged to innovate by the needs of our clients.
These challenges have driven us to develop and improve a range of equipment and design expertise that can meet the exacting demands of the dairy and infant formula industry.
Our Equipment
Automatic 25Kg Tipping
NZ Patent No. 540013 UK Patent GB2445682
“The Highest risk of foreign and pathogen contamination to any dairy powder is when it is exposed to a manual tipping operation.”
The HBD 25 has been designed specifically for the hygienic tipping of 25 kg Infant Formula Base and standard Whole Milk Powders.
Features
Hygienic in operation
Sealed system for maximum dust control
High product through put.(> 5500kg/hr)
Maximum product security
High yield
Ease of cleaning
Ease of operation
Ease of maintenance
Lights out capability.
UV 25 Steriliser Tunnel
Powder Projects UV 25 ultra violet light steriliser tunnel is specifically designed for the irradiation of 25kg plastic bags of various powders used in the production of Infant Formula.
Each UV tunnel is designed to customer particular requirements and independently validated with the 5 most common bacteria.
Features
Integrated air knife/bag cleaner on inlet
2 Stage conveyor insures 100% UV bag coverage
Log 3 Reduction bacteria count (99.9%) achieved
AssureQuality validation on 5 most common bacteria
Teflon coated UV tubes for glass breakage containment
Remote I/O for line control integration
Throughput > 240 x 25kg bags/hr
UV Intensity monitoring
Cat 3 Safety integration
Teflon UV lamp glass breakage protection.
Vacuum Blending
NZ Patent No. 735060
Powder Projects has recently developed a new blending method designed specifically for Infant Formula production.
The purpose of the design is to reduce the complexity typically involved in the production of dry blended infant formula.
Features
Combines powder transport, pre-gassing, blending, powder storage and controlled discharge In one vessel (blender).
Powder is gas preserved prior to blending giving optimal protection from oxidation of critical additives. This provides ‘industry best’ residual oxygen results.
Tapered Plug Valve Discharge (No bomb-bay doors).
No blend de-lamination due to powder moved in ‘plug flow’ format.
One short distance vacuum step followed by ‘plug flow’ discharge after blending directly to sifter then filler.
Low powder attrition due to minimal powder movement.
Filter-less vacuum transport step option available.
Continuous ‘just in time’ production 6000kg/hr with ‘one blender fill, one blender empty’ operation.
Industry best consistent blends with Constant of Variation < 5%.
Powder pre-gassed prior to blending minimal environmental oxygen exposure with powder preservation in minutes following tipping.
Powder blending can be halted or held for extended periods due to processing in a zero oxygen environment throughout the system.
CAS Sifter
Powder Projects has worked with local manufacturer CAS to develop a range of hygienically designed sifters purpose-built for Infant Formula production.
Features
Gas-tight for gas flooded operation
Easy open design with gas strut supported lid opening
Greater than 6000kg throughput
Design either linear or circular construction
Low profile for easy access for cleaning
2 piece fixed wire screens for easy handling (linear sifter only)
Roll away support frame
Pressure capable (Vacuum or Positive Pressure)
Ultrasonic screen cleaning capable.
Easy Clean Vacuum Vessels
Powder Projects has developed a range of ‘Easy Clean’ vacuum vessels. These vessels are available in multiple sizes depending on the application.
The vessels use standard pleated filters and are either seven or four filter configurations. No tools are required for access to the vessel filter assemblies.
Features
No tools are required for quick access
Gas struts for easy lid opening
Sonic Pulse filter cleaning
Stainless steel filter cages
Removable cell plate.
25kg Bag Sorting and Kraft Stripping
With Infant Formula blending plants being based predominantly on 25kg tipping, there has been a need for more sophisticated bag handling systems.
Powder Projects has ergonomically developed systems for the handling of 25kg bags from the depalletising through to the removal of the Kraft in preparation for transfer through to tipping.
Features
Auto bag sorting for product control
Waste kraft removal chutes direct to compaction
Gravity rollers for zero lift of bags
UV bag sterilisation following stripping.
Pre-Gassing
Powder Projects has developed a series of pre-gassing systems for residual oxygen reduction and preservation of dairy powders.
The systems can be either vacuum pre-gassing or percolating style depending on the process requirements.
Features
Integrated gas pressure control
Load cell weight control to ensure pre-gasser hopper remains at optimal powder level at all times
Gassing panel with rotameter gas flow modules for precise metering to gas injector probes
Oxygen and C02 metering with an integrated sample regime
PLC control with safety lock out
Optional gas recovery and recompression system.
Tower Blending Systems
The conventional blending tower method for Infant formula production has been the mainstay of Powder Projects.
We have completed the majority of the ‘large scale’ new plants built in the last 13 years in New Zealand.
Typically the process relies on 25kg bags of powder being tipped and then conveyed by vacuum to batch weigh vessels mounted above a Forberg style Twin paddle mixer.
Following blending the product is gravity fed through to sifting, pre-gassing then to can filling.
Features
Large vacuum vessels for blend batching with easy access for rapid plant turnaround
Fully de-mountable blending paddle drives
Powder Projects OEM vacuum ‘gain in weight’ batching system
Inert gas recovery system from pre-gasser
Gentle dense phase vacuum conveying to blender vacuum vessels for minimal powder breakdown.
Manual Bag Tips
Powder Projects has several manual bag tip designs that are used for various powder tipping applications.
The common theme in the design is ensuring that the dust created during the tipping is contained. This is achieved using large openings that provide ample area for air displacement and subsequent dust to be removed in a controlled manner.
Design Features Available
A load cell or solid mounting
Vibration or air shock hammer for powder flow
Integrated dust collection with pulse cleaning
Central dust collection connection
Above floor outlet for ground floor applications
Easy clean.
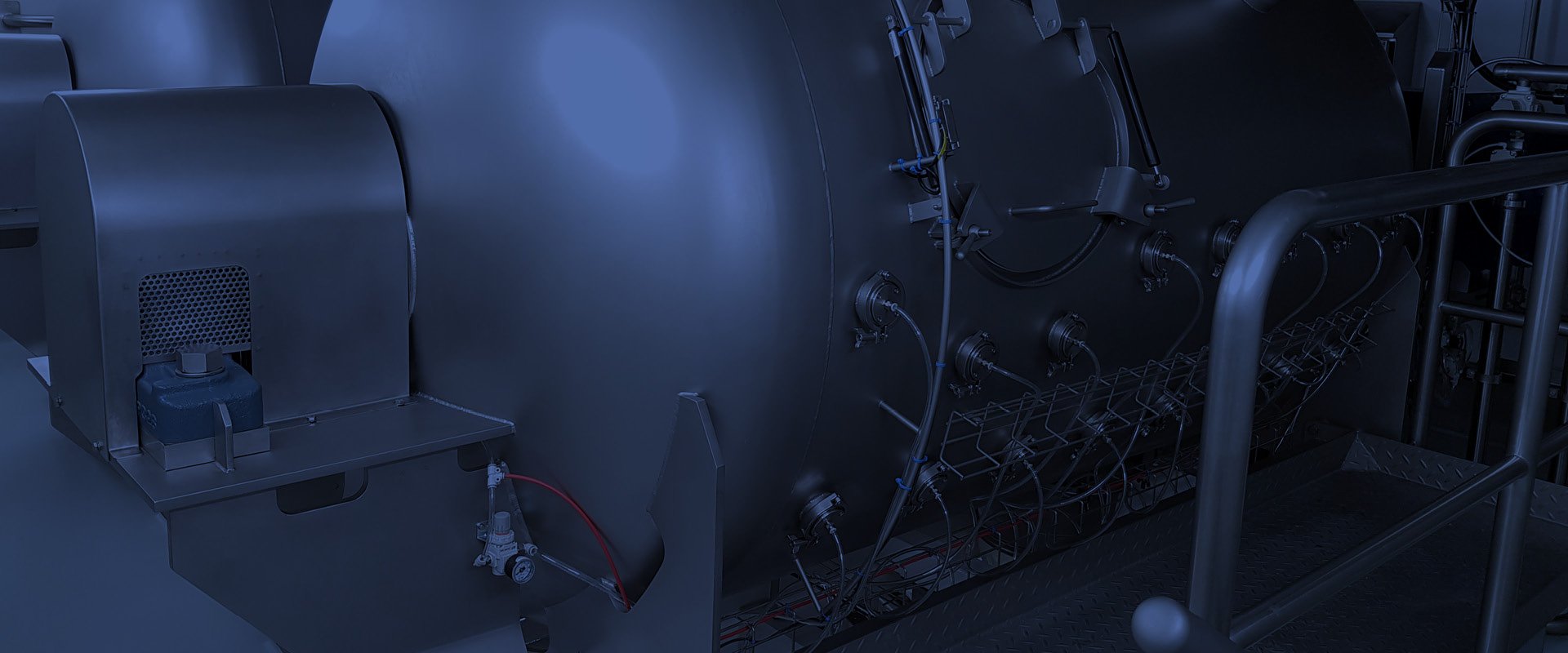